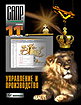
Опыт продвижения российской CAD/CAM-системы на западном рынке
Практически все отечественные CAD/CAM-продукты в той или иной мере известны на зарубежных рынках программного обеспечения.
Выход на зарубежный рынок диктуют следующие причины:
- желание подтвердить качество продукта и получить более широкое признание;
- позиционирование продукта, то есть поиск ниши в структуре мирового разделения труда и прибыли;
- приобретение опыта разработки и эксплуатации продукта в условиях новейших технологий, еще не получивших широкого распространения в России;
- расстановка приоритетов в направлениях дальнейшего развития продукта.
Все это справедливо и в отношении программного продукта ADEM (Omega technologies), опытом продвижения которого на европейский рынок мы и хотим поделиться.
Рассмотрим схему структуры европейского рынка на примере Германии, на которой приведены его основные участники, решающие конструкторские, технологические и комплексные задачи (рис. 1). Распределение систем по классам (легкие, средние, тяжелые) здесь довольно условно и отражает скорее уровень цен.
Первоначально предполагалось позиционировать систему ADEM в условно свободную нишу легких CAD/CAM, то есть позволяющих создавать чертежи, эскизы, 2D-модели и производить механообработку по двухмерным исходным данным. Наши исследования показывают, что более 80% объема конструкторско-технологических работ на машиностроительных предприятиях приходятся на решение двухмерных задач (2D-моделирование, черчение, 2D-механообработка). Так что теоретически мы выбрали наиболее плодотворную нишу для продукта. Однако проблемы, с которыми столкнулись наши дистрибьюторы в Европе, заставили нас пересмотреть первоначальные взгляды.
Практическое исследование европейского рынка выявило не только множество отличий, но и много общего с российским рынком. Вот наиболее характерные черты европейского пользователя, отмеченные нами:
- все желают получить готовое решение — систему с одной кнопкой «Выполнить»;
- все хотят мгновенно заменить уже имеющуюся технологию, внедрявшуюся длительное время (это видно по количеству специальных надстроек);
- существует строжайший контроль затрат на освоение и внедрение;
- изменение традиций проектирования допустимо только в случае заранее очевидного экономического эффекта (что маловероятно);
- техническое решение должно иметь «запас прочности», так, например, при приобретении 2D-системы решающим может быть вопрос о наличии возможностей 3D-моделирования;
- при высокой производительности труда и применении новейших технологий уровень подготовки пользователей оставляет желать лучшего;
- требуется бумажное обеспечение безбумажной технологии согласно стандарту ISO 9000;
- необходима интеграция САПР и АСУ.
На основе наших исследований был определен перечень технических требований к системе ADEM. В развернутом виде мы получили список почти из 100 новых задач.
Рассмотрим лишь самые принципиальные.
Интегрированность CAD/CAM. Вероятность успеха на европейском рынке нового CAD- или CAM-продукта ничтожно мала. Рынок CAD-систем в Европе заполнен до предела, например в Германии среди 2D-систем для машиностроения наибольшее распространение имеют AutoCAD и немецкая разработка MegaCAD. Конкурировать с локальной системой поддержки из-за рубежа довольно сложно и дорого, даже при значительных преимуществах продукта.
Универсальность системы к способу проектирования в плоскости и в пространстве. Сейчас довольно сложно найти предприятия, которые бы производили проектирование каким-либо одним способом. Тем не менее некоторые предпочитают производить механообработку по плоской модели, а другие — по объемной (рис. 2).
Быстрая и недорогая адаптация к существующему оборудованию. Подключение к станочному парку нужно производить с учетом специфических требований заказчика. Если данный процесс затруднен, то высокие расходы на адаптацию делают контракты убыточными.
Возможность подключения на промежуточном этапе проектирования. В отличие от России, где большинство предприятий созданы для обеспечения полного цикла проектирования, львиная доля предприятий Германии — подрядчики. Они практически не могут влиять на условия проектирования и формат передаваемых им заказчиком данных. Подрядчики работают с несколькими заказчиками, имеющими различный программный инструментарий. Поэтому система должна быть способна продолжить ведение «чужого» проекта. Например, на базе «чужих» моделей система должна обеспечивать создание оснастки и проведение механообработки.
Расчет на пользователя самой низкой квалификации. Система должна обеспечивать построение линейного процесса проектирования с минимумом логических переходов. Так, в случае замены специалиста для продолжения процесса конструкторско-технологической подготовки производства должно быть достаточно краткого инструктажа работника, не обладающего высокой степенью квалификации.
Быстродействие расчетных алгоритмов. Хотя расчет траектории движения инструмента для сложных деталей может занимать несколько сот часов, фраза «время — деньги» как нельзя более актуальна для Европы.
Получение заданного качества поверхностей. Недостаточно произвести обработку (пусть даже виртуальную) и после замеров и контроля изменить исходные данные, например глубину резания. Для сложных деталей нет времени на итерации. Следует заранее задать необходимое качество, а система должна гарантированно выполнить задание.
Контроль до выхода на станок. Контроль должен проводиться на всех уровнях — от CL-DATA до управляющей программы. Необходимы развитые средства визуального и численного контроля.
Подключение разнообразных баз данных — от стандартных изделий и инструмента до аналитических программ, разработанных самим заказчиком.
Логический анализ моделей. Система должна обладать средствами автоматического анализа модели для уменьшения числа исходных данных, вводимых пользователем.
Генерация протоколов работы в формах, разработанных заказчиком, и в соответствии с ISO 9000. С появлением указанного стандарта увеличился объем сопроводительной документации. Следовательно, появилась потребность в средствах полуавтоматической генерации разнообразных тексто-графических документов. Технически это привело к созданию модуля TDM (Technical Data Management), то есть изменилась формула продукта на CAD/CAM/TDM.
Если рассмотреть распределение возможностей продукта в спектре задач сквозного проектирования, то будет заметно наращивание функциональности в области объемного моделирования, пространственной механообработки и в части генерации технической документации. Следует подчеркнуть, что без этой модификации практически невозможно было продавать 2D-версию. Иначе говоря, для реализации «легкого варианта» продукту необходимо было стать системой среднего класса.
![]() |
Выводы
- Работать с зарубежными партнерами необходимо хотя бы для того, чтобы быть готовыми к завтрашнему дню на отечественном рынке.
- Постоянные «тренировки» помогают довольно быстро накопить «мышечную массу» программного продукта.
Виктор Силин, исполнительный директор
представительства Omega technologies Ltd в России
![]() |
Современные направления повышения производительности и качества изготовления изделий сложной формы
Интеграция в единую комплексную САПР
Сложность изделий, которые могут быть изготовлены на оборудовании с ЧПУ по программам, формируемым в современных CAM-системах, и, следовательно, чрезвычайно большой объем программ обусловили необходимость интеграции систем с оборудованием с ЧПУ. Поэтому состав программного обеспечения таких CAM-систем, наряду с возможностью вывода на перфоленту или записи управляющей программы на гибкий магнитный диск, может быть укомплектован программно-техническими средствами подключения станков с ЧПУ непосредственно к ПК. Вводится также дополнительный сервис, повышающий эффективность работы технологов-программистов и операторов станков с ЧПУ, — цеховой архив подготовленных управляющих программ и графический редактор управляющих программ.
Основная цель интеграции с технологическим оборудованием — повышение надежности управления станками вследствие исключения сбоев, характерных для работы с перфолентой, и сокращение общего количества механических устройств (перфоратор, фотосчитка, накопители на гибких магнитных дисках и др.).
Расширение использования САПР высокого уровня для рабочих станций и появление математических моделей для производства изделий с применением станков с ЧПУ поставили очередную задачу — сопряжение с ними CAM-систем среднего уровня. Применение таких интегрированных систем при достаточной функциональности CAM среднего уровня позволяет достичь минимальной стоимости программно-технических средств либо заметно сократить ее по сравнению с использованием только САПР высокого уровня.
Для примера рассмотрим реализованную с нашим участием систему проектирования аэродинамических моделей самолетов на одном из авиастроительных предприятий.
Аэродинамические модели, изготовляемые в обеспечение совершенствования характеристик создаваемых объектов авиационной техники, обладают повышенной сложностью формы поверхности, а также чрезвычайно высокими требованиями к точности изготовления. Но, при высокой функциональной сложности, конструкция модели характеризуется ограниченным объемом элементов. Трудоемкость и специфика ее разработки близки к формообразующей технологической оснастке (пресс-формы, штампы, литейные модели и формы и др.).
Центральное место в создании модели принадлежит формированию поверхности элементов модели и их аэродинамической компоновке. Для эффективного решения указанной задачи целесообразно использовать все возможности, предоставляемые современной вычислительной техникой и программным обеспечением, и именно на это ориентированы САПР высокого уровня.
Поскольку полный набор функций проектирования реализуется в САПР высокого уровня для разработки конструкции, допустимо использование специализированных систем с определенным ограничением функций, ориентированных на ПК.
Построение системы на основе рационального сочетания ограниченного числа рабочих мест САПР высокого уровня и специализированных конструкторских и технологических систем для ПК, которое соответствует техническим особенностям объектов, подлежащих разработке и изготовлению, позволило более чем в 10 раз сократить расходы на автоматизацию по сравнению с ее проведением на базе одной из САПР высокого уровня.
![]() |
Повышение точности изготовления изделий сложной формы
Совмещение в единой системе средств CAD/CAM различного уровня обеспечило (при минимальных затратах на введение автоматизации) сочетание наиболее развитых возможностей моделирования технических объектов в комплексные CAD/CAM с простотой эксплуатации и высокой эргономичностью специализированных конструкторских и технологических систем для ПК.
Решение задачи комплексной автоматизации на базе современных программно-технических средств создало условия для совершенствования сложившейся технологии использования оборудования с ЧПУ. Важнейшими направлениями в современных условиях стали как повышение точности и чистоты станочной обработки, снижающей трудоемкость последующей ручной слесарной обработки, так и рост производительности станочного оборудования.
Наряду с повышением характеристик станков и режущего инструмента существенное значение приобретает совершенствование подготовки управляющих программ на обработку изделий сложной формы. В настоящее время, в условиях широкого предложения высококачественного инструмента, вследствие высокой стоимости формообразующей технологической оснастки и экспериментальных моделей технически и экономически целесообразно применение для финишных операций фрезы с фабричной заточкой и аттестованными геометрическими параметрами.
Нынешние достижения в области разработки твердосплавного инструмента для фрезерования инструментальных сталей (они являются основным материалом формообразующей технологической оснастки и элементов аэродинамических моделей) позволяют перейти при съеме припуска 0,5-2 мм от традиционных рабочих подач 80-100 мм/мин к величинам около 1000 мм/мин. Требуемая скорость вращения шпинделя должна составлять 1000-3000 об./мин. Этот диапазон подач и скоростей вращения шпинделя характеризует станочное оборудование конца 80-х годов на большинстве предприятий России. Поэтому освоение перспективного инструмента и режима обработки, которые в 4-10 раз повышают производительность, является чрезвычайно актуальным.
Типовое представление траектории движения инструмента при фрезерной обработке сложной поверхности — кусочно-ломаная линия, аппроксимирующая обрабатываемую поверхность. Два сопрягаемых отрезка траектории (укрупненно) показаны на рис. 3. При увеличении подачи в угловой точке траектории происходит возрастающий «заброс» — отклонение инструмента от заданной траектории вследствие люфтов и ограниченных динамических характеристик станка, определяемых его жесткостью, параметрами системы управления и др. Проведенные нами эксперименты показали, что отклонения от траектории зависят как от угла излома траектории, так и от величины подачи.
Обработка с ограничением динамических погрешностей («забросов») в угловых точках траектории потребует снижения подач в окрестности угловых точек. Для изготавливаемых деталей это приведет к снижению реальной подачи в два-три раза. Чтобы исключить динамические погрешности при сохранении заданной подачи, углы между сопрягаемыми отрезками траектории должны приближаться к 180о. Такие значения углов могут быть достигнуты за счет дополнительного уменьшения длин линейных участков траектории и соответствующего возрастания объема управляющей программы.
Рост объема управляющих программ, характерный для высокоточной и высокоскоростной обработки, приводит также к заметному увеличению времени ввода управляющей программы в УЧПУ и ее «электронной» обработки, выполняемой УЧПУ при формировании управляющих воздействий для приводов станка.
Вышеуказанные проблемы обеспечения высокоскоростной обработки на станках с ЧПУ определяют реализацию взаимодействия с конкретными системами управления ЧПУ и станками. Их решение связано, с одной стороны, с использованием внутренних возможностей интерполяции кривых, заложенных в УЧПУ, и на этой основе — с заменой ломаных траекторий движения инструмента гладкими аппроксимационными кривыми, создающими условия для бездефектной обработки с повышенными подачами, при одновременном сокращении объема управляющих программ. С другой стороны, необходимо развитие программно-технических средств сопряжения ПК с УЧПУ станков, обеспечивающих загрузку (параллельную с обработкой) управляющих программ и режим сегментированной загрузки («подкачку») программ большого объема по мере их выполнения. Данные решения получили отражение в виде программно-технических средств прямого управления станками с ЧПУ в составе системы ГеММа-3D.
![]() |
Контроль точности изготовления
Сейчас, при внедрении средств автоматизации проектирования и производства, чрезвычайно актуальна оценка точности изготовления изделий. Прежде всего такая оценка существенна для формообразующей технологической оснастки (пресс-формы, штампы, литейные формы и др.): во-первых, от точности изготовления зависят последующие затраты на доработку продукции массового производства, изготавливаемой на данной оснастке (удаление облоя, пригонка элементов изделий при сборке и т.д.), во-вторых, она определяет внешний облик и качество изделий в соответствии с замыслом дизайнера, зазоры в местах сопряжения деталей, внешний вид.
Важнейшим требованием к результатам измерений, кроме оценки точности производства, является также оценка качества составляющих производственного процесса. Как говорят за рубежом: «Не важно, как ты делаешь, а важно, как ты контролируешь выпускаемую продукцию».
Современные измерительные машины представляют собой высокоточные устройства, обеспечивающие пять степеней свободы при ориентации измерительного щупа в пространстве. Управляемые от ПК, они комплектуются развитыми библиотеками программ для проведения измерений геометрических параметров технических объектов различной формы и для обработки результатов измерений. Наиболее освоены измерения типовых геометрических объектов, таких как плоские криволинейные контуры, плоскости, призмы, тела вращения и др. Вопросы обработки измерений указанных объектов, обеспечивающих описание преобладающего объема изделий общего машиностроения, в полном объеме рассмотрены в современной литературе. Однако проведение измерений и обработка их результатов применительно к изделиям сложных форм до настоящего времени представляют существенные трудности.
Во-первых, при установке изделия, подлежащего замеру, неизбежны ошибки базирования, обусловливающие некоторое несовпадение осей изделия с осями исходной математической модели его поверхности.
Во-вторых, практически невозможен непосредственный замер координат контролируемых точек изготовленной поверхности, отклонения которых от эталона должны быть установлены. Они могут быть установлены только косвенно, на основании измерений достаточно большого объема в их окрестности.
В-третьих, при обработке результатов измерений необходимо учитывать конечные размеры мерительного щупа, с одной стороны, ограничивающие доступ к отдельным участкам поверхности, а с другой — не позволяющие однозначно установить точку касания измеряемой поверхности.
Эти проблемы решены в метрологическом модуле системы ГеММа-3D. Возможности системы по измерению изделий сложной формы и обработке их результатов позволили включить ее в качестве базового программного обеспечения в измерительные машины нетрадиционного типа. В их числе — измерительная машина типа ВАРИАКС с шестью подвижными тягами, обеспечивающими перемещение платформы с мерительным инструментом (г. Саратов, главный конструктор А.Г.Лаптев), лазерная эхометрическая установка для измерения крупногабаритных изделий (г. Москва, НИИОФИ), бесконтактная фотограмметрическая система измерения сложных профилей в массовых производствах.
Владимир Вермель,
начальник отдела ЦАГИ, научный
руководитель разработки системы ГеММа-3D
![]() |
Лазерные технологии быстрого изготовления прототипов
Современные системы компьютерного проектирования (CAD) позволяют значительно сократить затраты времени и средств на разработку и конструирование новых изделий. Однако проблема изготовления первого физического образца (и даже отдельной детали для изделия сколько-нибудь сложной формы) остается наиболее «узким местом», поскольку разработка технологии изготовления детали и соответствующей оснастки зачастую требует затрат, сопоставимых со стоимостью разработки самого изделия.
Примерно с начала 80-х годов начали интенсивно развиваться новые технологии формирования трехмерных объектов — не путем удаления материала (точение, фрезерование, электроэрозионная обработка) или изменения формы заготовки (ковка, штамповка, прессовка), а путем постепенного наращивания материала или изменения фазового состояния вещества в заданной области пространства. На данный момент значительного прогресса достигли технологии послойного формирования трехмерных объектов по их компьютерным моделям. Эти технологии наиболее известны как RP&M (Rapid Prototyping and Manufacturing), или просто RP (Rapid Prototyping), FFFF (Fast Free Form Fabrication), либо как CARP (Computer Aided Rapid Prototyping). Термин «быстрое прототипирование» (Rapid Prototyping, RP) сейчас пользуется большой популярностью во многих отраслях, например в разработке программного обеспечения, в электронной промышленности и т.д.
Необходимо отметить, что в настоящее время технологии быстрого изготовления прототипов являются частью идеологии Time-Compression Engineering, при этом рассмотрению подвергаются все стадии разработки новых изделий — от появления идеи до выхода на рынок.
С точки зрения конструкторов невиртуальных объектов, быстрое прототипирование означает быстрое прямое преобразование компьютерных моделей в физический, осязаемый объект. Другие названия RP также подтверждают это: настольное производство (Desktop Manufacturing), трехмерный принтер (3D printing) или плоттер и т.п. В большинстве случаев использование RP приводит к получению формы или модели, которая используется для подготовки реального производства. В некоторых случаях полученный объект просто используется конечным пользователем, причем доля такого использования с каждым годом растет, в связи с чем термин «прототипирование» становится не совсем точным.
Эффект от использования RP проявляется в значительном, в десятки раз, сокращении времени и затрат на разработку новых изделий, а также в повышении качества разработки. Конструктор получает рабочую модель почти так же легко и быстро, как чертеж с принтера или плоттера, что позволяет значительно повысить эффективность работы. Во всем мире число установок RP составляет десятки тысяч, и их число быстро растет. Крупные компании, как правило, эксплуатируют до десятка установок, более мелкие пользуются услугами специализированных центров.
Как правило, под RP понимают технологии послойного изготовления трехмерных объектов, хотя наша практика показывает, что почти все традиционные технологии резки листовых материалов можно с успехом использовать для разработки и производства достаточно сложных трехмерных изделий, таких как металлические шкафы или элементы оформления витрин.
![]() |
Послойное выращивание
В настоящее время быстро развиваются технологии послойного изготовления трехмерных объектов, которые основаны:
- на лазерной резке листовых материалов;
- спекании и наплавке порошков металлов, керамики и полимеров лазерным излучением или электронным пучком;
- экструзии термопластиков;
- фотоинициированной лазерным излучением или излучением ртутных ламп полимеризации.
![]() |
Лазерная стереолитография
Чаще всего используется технология, основанная на использовании фотополимеризации лазерным излучением. Такой процесс был первым процессом RP, который использовался в серийно выпускаемых установках (фирмы 3Dsystems). Технология, получившая название «лазерная стереолитография» (ЛС, Laser Stereolithography), несмотря на появление других технологий, остается наиболее широко используемой и имеет наилучшие технические показатели. Лазерная стереолитография позволяет получать самые точные и сложные модели, а используемые в ЛС материалы обладают рядом преимуществ: прочность, прозрачность, влагостойкость, легкость обработки поверхности, возможность склейки и т.д.
ЛС получила свое развитие и в России. В Институте проблем лазерных и информационных технологий (ИПЛИТ) РАН разработаны и действуют несколько экспериментальных и опытных установок.
Одним из наиболее важных этапов создания образца является процесс подготовки управляющей программы, предусматривающий (рис. 4):
- компьютерное моделирование детали и сохранение модели в STL-формате (этот формат данных поддерживают AutoCAD, EUCLID, CATIA, Power Solution и другие системы);
- разбиение полученного компьютерного образа на тонкие слои с заданным шагом;
- расчет траектории лазерного луча, заполняющей каждое сечение.
После того как управляющая программа получена, можно приступать к послойному изготовлению прототипа (детали). Для этого используется лазерная установка с ванной, оборудованной специальным столом. Эту ванну заполняют жидкой фотополимеризующейся под воздействием лазерного луча композицией (ФПК). Спекание материала выполняется послойно перемещением лазерного луча по заданной программе. По завершении обработки первого слоя стол ванны опускается на шаг и выполняется формирование следующего слоя. Так, шаг за шагом, формируется деталь.
![]() |
Использование
Исходные данные для стереолитографии с использованием установки ЛС250/Э ИПЛИТ РАН могут быть представлены в виде:
- эскизов и чертежей на бумажном носителе;
- файлов трехмерных объектов в формате STL, DXF или IGES;
- файлов компьютерных томографов, координатно-измерительных машин и т.д.
Объекты, созданные лазерной стереолитографией, могут быть использованы следующим образом (рис. 5, 6):
- как конструкторские и дизайнерские прототипы при создании макетов изделий и сборок. При этом обеспечивается возможность визуализации газо- и гидродинамических потоков внутри модели;
- в качестве формообразующей оснастки при различных видах точного литья (в частности, для изготовления формообразующей оснастки из других материалов по созданным моделям);
- как мастер-модели при изготовлении электродов для электроэрозионной обработки;
- для исследовательских работ по созданию биосовместимых имплантантов;
- при восстановлении объектов по данным компьютерных томографов, координатно-измерительных машин и других видов зондирования трехмерных объектов для целей медицины, криминалистики, археологии и др.
![]() |
Параметры и ограничения
Лазерная стереолитография позволяет получить очень сложные цельновыращенные модели. Ограничения по форме обусловлены практически только невозможностью вырастить детали с полностью изолированными внутренними полостями. Точнее, вырастить-то можно, но при этом в полости останется неудаленная фотополимеризующаяся композиция. Образно говоря, мы получаем запечатанную, выращенную путем ЛС бутылку, внутри которой неспекшаяся жидкая масса.
Точность изготовления моделей определяется так:
- по оси Z — толщиной слоя, как правило, составляющего 0,1-0,2 мм (толщина слоя зависит от свойств используемого материала);
- по осям Х и Y — размером пятна лазерного излучения, динамической точностью позиционирования пятна и свойствами материала (минимальная толщина стенки — 0,2 мм, программная точность воспроизведения — 0,01 мм);
- усадкой и деформацией материала. При правильном подборе параметров процесса отклонения не превышают 0,1 мм.
Немаловажным ограничением в использовании ЛС является стоимость самой установки и ее компонентов, в том числе и стоимость ФПК — основного расходного материала. Однако с течением времени стоимость основных компонентов снижается, причем стоимость отечественных ФПК существенно ниже импортных.
Размеры выращиваемых деталей ограничены главным образом размерами ванн для ФПК, которые обычно имеют размеры куба со стороной в 100, 250, 350 или 500 мм. Для получения более крупных деталей идут по пути выращивания отдельных секций с последующим их склеиванием.
Евгений Коцюба,
ведущий специалист ИПЛИТ РАН
***
Помимо приведенных выше докладов, интересные сообщения, на мой взгляд, были сделаны Евгением Кукареко, техническим директором компании OmegaSoftware GmbH, тесно сотрудничающей с известным российским системным интегратором компанией «АйТи» (более детально свои идеи автор изложил в статье «Управление инженерными данными в автоматизированной системе управления предприятием», опубликованной в данном номере), исполнительным директором компании «Лоция Софт» Николаем Ширяевым («Системы автоматизации технического документооборота и управления проектными данными (TDM/PDM) на российском рынке. Реализация систем, опыт внедрения, перспективы развития»), а также специалистом «Русской Промышленной Компании» Владимиром Голевым («Организация аппаратного комплекса отдела САПР предприятия»). К сожалению, два последних сообщения были представлены в редакцию в виде тезисов, не дающих исчерпывающей информации по заявленным темам, поэтому мы не приводим их в данной публикации.
В заключение предлагаем всем участникам секции «Автоматизация проектирования и подготовки производства», состоявшейся 27 сентября в рамках конференции «Информационные технологии в России XXI века» на SofTool’2000, присылать свои критические замечания, пожелания по организации дальнейшей работы секции, а также заявки по темам, о которых наши читатели хотели бы получить больше информации как в рамках самой конференции, так и на страницах журнала «САПР и графика». Для этого можно воспользоваться одним из указанных электронных адресов: andrmaz@aha.ru или mazurin@compress.ru.
«САПР и графика» 11'2000